2017 Archived Content
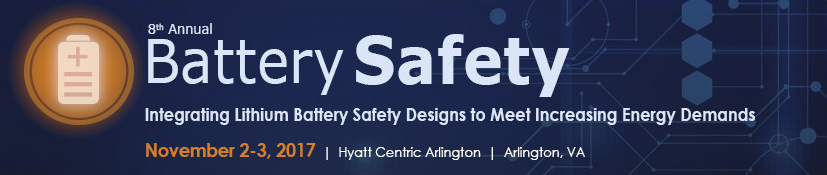
Higher energy and higher use lead to higher risk. While research continues to boost the energy storage capability of lithium-ion batteries (LIBs) and leads to expanding applications and consumer use, the task of implementing effective safety strategies
falls on regulatory authorities, cell manufacturers, R&D engineers and forensic scientists. Accurate tests and models are critical for predicting and controlling the complex electrochemical, thermal and mechanical behavior of LIBs while forensic
investigations and regulations are required for safe transport. The Battery Safety 2017 conference continues this vital dialogue to integrate and implement LIB safety to meet ever-increasing energy demands.
Final Agenda
Tuesday, October 31
5:30-8:30 pm Dinner Workshop*
W2: Battery Safety Training Tutorial
Instructor: Shmuel De-Leon, CEO, Shmuel De-Leon Energy, Ltd.
*Separate registration required.
Wednesday, November 1
5:00 pm Registration for Battery Safety Conference
5:30 Welcome Reception in the Exhibit Hall with Poster Viewing
6:30 Close of Day
Thursday, November 2
8:00 am Morning Coffee
8:30 Organizer’s Welcome
Mary Ann Brown, Executive Director, Conferences, Cambridge EnerTech
8:35 Chairperson’s Opening Remarks
Judith Jeevarajan, Ph.D., Research Director, Electrochemical Safety, Underwriters Laboratories, Inc.
8:45 FEATURED PRESENTATION: Increasing the Intrinsic Safety of Lithium-Ion Batteries
Falko Schappacher, Ph.D., Managing Director and Head, Cell
System Division, MEET Battery Research Center, University of Münster
There are several ways to increase the safety of lithium-ion batteries. Measures can be taken on the system (BMS) or cell level (CID, PTC) to overcome critical events like overcharge or external short circuit, but when it comes to an internal failure,
these measures are not effective. Hence it is important to increase the intrinsic safety of LIB on the chemistry level.
9:20 Battery Safety: A Materials Chemistry Perspective
Arumugam Manthiram, Ph.D., Director, Texas Materials Institute;
Professor, Mechanical Engineering, University of Texas at Austin
The intrinsic chemistry of the electrode and electrolyte materials used in a battery as well as cell engineering will have a profound influence in controlling battery safety. This presentation focuses on the role of materials chemistry, particularly bulk
composition, surface composition, electrode-electrolyte interaction, chemical species crossover from one electrode to another, and metal-dendrite formation and growth.
9:55 The Road to Safe, High-Performance Energy Storage Is Paved with Zinc
Joseph F. Parker, Ph.D., Research Chemist, Chemistry Division, U.S. Naval Research Laboratory
Lithium-ion dominates the energy storage landscape yet remains under threat of catastrophe. Zinc batteries also provide high specific energy while countering with the inherent safety of aqueous electrolytes. Traditional zinc anodes suffer from suboptimal
capacity and cyclability, forming short-inducing dendrites upon charging. We redesigned the zinc as a “sponge” architecture that achieves >95% theoretical capacity and dendrite-free cycling.
10:30 Coffee Break in the Exhibit Hall with Poster Viewing
11:00 FEATURED PRESENTATION: Battery Diagnosis and Prognosis for Battery Safety Design and Mitigation
Boryann Liaw, Ph.D., Department Manager, Energy Storage and Advanced Vehicles,
Idaho National Laboratory
Lithium-ion batteries (LIBs) continue to play a prevailing role in energy storage and power source applications. As performance requirement and specification become more demanding, the battery system configuration and integration are getting complicated
as well. It is inevitable that battery performance, durability, reliability and safety issues thus continue to escalate as great concerns among end users, system integrators, battery manufacturers and regulators. Addressing these battery performance
issues may require a more advanced approach than what is perceived today. For instance, the traditional design of experiments, optimization and testing might not be able to provide the precision and accuracy in validating battery design parameters
to ensure the desired performance requirements are met for durability, reliability and safety in operation. Battery failure mode and effect analysis could provide the enabling techniques to address these battery performance issues. Successfully implementing
such practices requires an advanced battery diagnosis and prognosis approach. This presentation is intended to discuss this aspect and to explain what would it take to establish such diagnostic and prognostic capabilities currently undertaken at Idaho
National Lab.
11:35 FEATURED PRESENTATION: Thermal Runaway Modeling of Lithium-Ion Battery Abuse
Ahmad Pesaran, Ph.D., Chief Energy Storage Engineer, National Renewable
Energy Laboratory
12:10 pm Non-Chromium Soft Packaging Without Chromate Treatment
Masa Tatewaki, Vice President, Toppan USA, Inc.
Along with the increase of lithium ion battery consumption, the issue also raised how to dispose of those battery without impacting the environment. REACH-SVHC already announced Sunset date for Sodium dichromate and chromic anhydride as 9/21/2017. In
this session, review current material issue; Chromate compound has been used for lithium ion packaging and present a solution without using Chromate treatment.
12:40 Session Break
12:45 Luncheon Presentation (Sponsorship Opportunity Available) or Enjoy Lunch on Your Own
1:15 Session Break
2:00 Chairperson’s Remarks
Boryann Liaw, Ph.D., Department Manager, Energy Storage and Advanced Vehicles, Idaho National Laboratory
2:05 FEATURED PRESENTATION: Characterizing Battery Failure Using Multi-Scale X-Ray Imaging
Paul Shearing, Ph.D., Reader, Chemical Engineering & Materials, Department
of Chemical Engineering, University College London
Battery electrode materials are complex hierarchical structures, where heterogeneities at microscopic length scales are thought to drive macroscopic failure mechanisms. As these materials are likely to evolve over time, in response to a range of processing
and environmental conditions the relationship between the electrode microstructure and the cell performance evolves: understanding how these changes in microstructure can be linked to understanding of degradation and failure is pivotal to improving
device lifetime and safety. The increasingly widespread use of tomography has revolutionized our understanding of these materials. With increasing sophistication researchers have been able to characterize samples over multiple time and length scales
from nm to mm and from ms to days. Here we consider examples of our work to explore these materials in three and "four" dimensions, presenting case studies ranging from characterization of transport phenomena at nano-meter length scales, to exploring
battery failure at millisecond time scales with a particular focus on the use of these tools to understand degradation and failure processes.
2:40 FEATURED PRESENTATION: Nano-Photonic Polymer Sensors for Enhanced Battery State Monitoring
Wolfgang Schade, Ph.D., Head of Department, Fiber Optical Sensor
Systems, Fraunhofer Heinrich Hertz Institute
3:15 Lithium-Ion
Battery Thermal Management Solution to Prevent Temperature Damage to Cells and Thermal Runaway Propagation
Michael Mo, CEO, KULR Technology
Battery overheating can cause permanent damage to cells and thermal runaway propagation throughout battery pack. Lithium metal plating, which occurs in cold temperature, can cause rapid aging of battery cells through electrolyte decomposition. KULR Technology
presents a carbon fiber based thermal management solution that can heat and cool battery packs and prevent thermal runaway propagation.
3:30 Refreshment Break in the Exhibit Hall with Last Chance for Poster Viewing
4:10 An Update on the DOE OE Energy Storage Systems Safety Roadmap – Supporting a Goal of Fostering Confidence in the Safety and Reliability of ESS
Summer Ferreira, Ph.D., Principal Member, Technical Staff, Sandia
National Laboratories
This presentation provides information on the Roadmap recently revised by the Working Group on Energy Storage Systems safety. This roadmap provides direction and strategy on efforts including research and development priorities, safety codes and standards
development and revision, and collaboration activities for system stakeholders.
4:40 A Comprehensive Study on the Safety of Aged Li-Ion Cells and Modules
Judith Jeevarajan, Ph.D., Research Director, Electrochemical
Safety, Underwriters Laboratories, Inc.
The stationary energy storage industry has initiated the installation of Li-ion batteries that had been used in automotive applications. This is a second life for the ‘once-used’ Li-ion batteries. However, there is insufficient data on this
type of second use of aged Li-ion batteries, especially with respect to the safety. Underwriters Laboratories in collaboration with Texas A&M University has carried out studies to cycle cells and modules under different voltage ranges as well
as under the hybrid electric vehicle profile at different temperatures. The fresh and cycled cells and modules were subjected to off-nominal tests such as overcharge and external shorts to understand the characteristics of the aging process and how
it might affect safety. Destructive analysis was carried out on fresh and cycled cells to understand component level changes that occur during the aging process. The results of the test program will be presented in this talk.
5:10 Close of Day
5:30-8:30 Dinner Workshop*
W4: How to Qualify Your Battery Suppliers to Prevent Failures and Thermal Events
Instructor: Vidyu Challa, Ph.D., Technical Director, DfR Solutions
*Separate registration required.
Friday, November 3
8:00 am Battery Breakfast Breakout Discussion Groups
Grab coffee and breakfast and join a discussion group. These are moderated discussions with brainstorming and interactive problem solving, allowing conference participants from diverse backgrounds to exchange ideas and experiences and develop future
collaborations around a focused topic.
9:00 Chairperson’s Remarks
Ahmad Pesaran, Ph.D., Chief Energy Storage Engineer, National Renewable Energy Laboratory
9:05 Thermal Design & Simulation of a Natural Convection Cooled 12V Li-Ion Battery
Kem M. Obasih, Ph.D., Technical Leader, Thermal, Advanced Power Solutions,
Johnson Controls - Power Solutions
The design of a 12V Li-ion battery must ensure adequate thermal management for safe operations. Heat generation rates of the cell jellyrolls during all modes of operation are required for use in battery thermal simulations. Performance of thermal
and flow simulation of the battery during normal and abuse operations are essential to ensure the battery meets safe temperature and pressure operation specifications.
9:35 Vehicle Electrification: A123 Systems’ R&D Approach for Low- and High-Voltage Material Development
Maha Hammoud, Ph.D., R&D Manager, Materials Engineering, A123 Systems, LLC
A123’s advanced chemistry and system design has driven our low-voltage lithium-ion battery to industry leadership for both 12V (Starter Battery) and 48V (Auxiliary Battery) applications. The advanced chemistry contains A123’s patented
Ultraphosphate™ (LFP) cathode powder, for which a fundamental approach to design the material at the crystal structure has yielded superior performance over our competitors. A123 is implementing the same fundamental material development
approach for high-voltage applications. This approach is yielding high-energy density cells utilizing nickel-rich NCM cathodes and high-capacity anode materials that are thermally more stable under abuse conditions. This presentation topic is
therefore focused on the high-power material development that has resulted in LiSBs with cold crank capabilities that surpass lead-acid batteries and high-energy advancements at the material and cell level to achieve energy densities approaching
300 Wh/kg and 600 Wh/L for EV applications while maintaining the needed safety performance.
10:05 Safecore Technologies: A New Revolution for Lithium-Ion Battery Safety
Jiang Fan, Ph.D., President, American Lithium Energy Corporation
With recent recalls of consumer products and safety incidents in flights, Li-ion batteries have become an urgent public safety issue. Up to this point, good safety solutions often adversely affect battery performance. For instance, some fire-retardant
electrolytes can protect the battery from the fire in the internal short, but it also kills the battery cell life. In this talk, a new battery cell safe design concept called SafecoreTM will be presented. The cell with SafecoreTM will have a “circuit breaker” that can protect the cell from thermal runaway when the battery cell is overcharged or internally shorted due to BMS failure, manufacturing defect, or outside impact. The circuit breaker is a safe layer
inside the cell, which will be activated by the heat, voltage, and current to break the electrodes so as to interrupt the overcharge current or internal short current. The properly engineered safe layer will not interfere with any electrochemical
reaction and hence have no effect on normal cell performance like cycle life.
10:35 Coffee Break
11:00 Battery Design Impacts on Thermal Runaway Severity under Worst-Case Test Conditions
Thomas P. Barrera, Ph.D., President, LIB-X Consulting
Lessons learned from industry battery thermal runaway incidents indicate that worst-case testing in a relevant configuration and environment is necessary to properly determine safety risk. Worst-case testing includes detailed consideration to the
battery electrical, mechanical, and thermal design interfaces employed in the intended application. Safety test results from a heritage NASA non-rechargeable lithium battery indicate that battery design, test protocols, and environments have a
significant impact on thermal runaway severity.
11:30 Merits of the Cell Bottom Vent Feature in 18650 Cells for Preventing Side Wall Rupture
Eric C. Darcy, Ph.D., Battery Technical Discipline Lead, Power Systems Branch,
NASA Johnson Space Center
Using an NREL-/NASA-patented on-demand internal short circuit device imbedded in a series of 18650 cell designs with and without bottom vents and with and without thicker can walls, our thermal runaway tests indicate that both features reduce a cell’s
propensity to side wall rupture. The results of thermal runaway calorimeter and very high-speed X-ray videography give us unique insight as to why and which feature is more effective.
12:00 pm Session Break
12:15 Luncheon Presentation (Sponsorship Opportunity Available) or Enjoy Lunch on Your Own
12:45 Session Break
1:30 Chairperson’s Remarks
Kevin Fok, Senior Project Manager, LG Chem Power, Inc.
1:35 Thermal Runaway of Lithium Batteries Analyzed by Accelerating Rate Calorimetry and Thermography
Carlos Ziebert, Ph.D., Senior Scientist, Head of the KIT Battery Calorimeter Center, IAM-AWP, Karlsruhe Institute of Technology
Extensive market penetration of electric vehicles and stationary storage systems requires use of safe lithium-ion batteries. Thermal runaway of Li-ion cells in a larger battery pack, especially, is the worst case which must be avoided. To get detailed
insight into the exothermic reactions triggering thermal runaway, results from accelerating rate calorimetry, thermography and pressure measurements will be presented.
2:05 Quantification of Thermal Hazards Associated with Lithium-Ion Batteries
Stanislav I. Stoliarov, Ph.D., Associate Professor,
Fire Protection Engineering, University of Maryland
The key aspect defining safety of lithium-ion batteries is the amount of thermal energy that they release upon failure. In the current study, a new experimental technique, Copper Slug Battery Calorimetry, was developed to simultaneously quantify
the energy released inside an LIB cell (resulting in increasing cell temperature) and outside the cell (associated with flaming combustion of ejected battery materials). A relationship between these parameters and cascading failure of battery
packs was analyzed.
2:35 Mythbusting Battery Fire Investigation
Joseph (Joe) Nowikowski, MSEE, PE, CFEI, Electrical
Division Manager, Western Region, Rimkus Consulting Group, Inc.
Lithium batteries have been involved in fires, often being immediately assumed as the cause. However, many people do not understand the rigors of proving fire causation and identifying those ultimately responsible for its costs. This presentation
focuses on the comprehensive analysis that makes up the investigative end of battery failures and fires.
3:05 PANEL DISCUSSION: First Responders
Much of this meeting has centered on testing and transportation of batteries prior to installation. However, attention must be focused on what protective systems may be needed to both prevent and safely mitigate a fire. Hear from this panel of
experts as they share the prevention and response tactics that reduce risk to occupants, first responders, and structures.
Moderator:
Kevin Fok, Senior Project Manager, LG Chem Power, Inc.
Panelists:
Paul Rogers, Fire Department NYC
Matthew Paiss, Fire Captain, San Jose Fire Department
Nicholas Warner, Senior Test Engineer, Energy
Advisory Laboratory Services, DNV GL
Brian O’Connor, Fire Protection
Engineer, National Fire Protection Association
4:05 Conference Wrap-Up
Mary Ann Brown, Executive Director, Conferences, Cambridge EnerTech
Kevin Fok, Senior Project Manager, LG Chem Power, Inc.
4:15 Close of Battery Safety Conference